What is Reverse Logistics?
Reverse logistics is the process of sending goods back up the supply chain from end users to either the producer or the retailer. Offering returns to your consumers is just smart business, whether the client is returning products they don’t need, the product has reached the end of its life cycle, or the product is broken or defective. Reverse logistics is used in this situation. This procedure also applies when products need to be thrown away or recycled, and it covers the case in which the final user oversees the product’s refurbishment, disposal, or even resale.
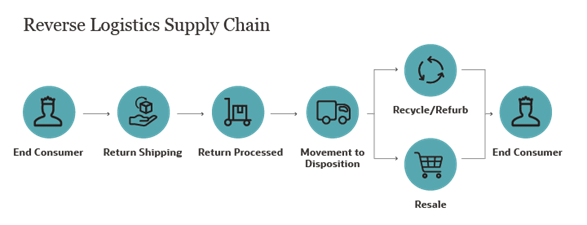
Difference Between Reverse Logistics VS Traditional Logistics
Traditionally, a manufacturer or distributor comes after the suppliers in the product flow. From retailers, the goods are subsequently delivered to clients. To return items to any point along the supply chain, reverse logistics management starts with the customer and works backward.
Well-planned supply chains can manage some requirements for reverse logistics and are adaptable to changes. Using this reverse procedure, products can be returned to the original supplier or one level further along the supply chain. Even regular sales or discount channels (like liquidators) may receive returned goods.
When is the reverse logistics process used?
When items return from their destination back through the supply chain to the seller and maybe back to the suppliers, organizations utilize reverse logistics. The product must be sold or at least have some of its value recovered. With the growth of e-commerce, returns, which are worth nearly one trillion dollars globally annually, have become more common.
Recovering value and encouraging consumer repurchase are the goals of reverse logistics. At least 30% of things ordered online are returned, compared to less than 10% of in-store transactions. Reverse logistics is a sophisticated tactic employed by astute companies to boost repeat business and client loyalty while lowering return-related losses.
Managing returns and acquiring surplus supplies and resources are steps in the reverse logistics process. The procedure is also in charge of handling any leases or renovations. Reverse logistics differs among businesses, and there are various financial incentives to enhance reverse logistics management.
Empty tap containers are used in the reverse logistics process, for instance, in the beverage business. The goal of beverage-producing companies is to reuse their containers to recoup their original cost. Transportation must be planned, shipping loads must be managed, and containers must be cleaned.
How does it work?
Reverse logistics is a process used in the building industry to transport and recover salvaged materials. Reverse logistics presents a chance for cost savings as the building sector implements more environmentally friendly practices to cut waste.
In the food industry, reverse logistics oversees managing pallet returns and packing materials. Businesses must also deal with declined food deliveries. As a result of delays that allow food to expire and concerns about tampering, rejections might result in logistical issues. To address these logistical issues, the Reverse Logistics Association is creating secure, quick, reliable, login (SQRL) codes for use on product packaging.
5 Easy Steps to Reverse Logistics
1. Process The Return:
The return procedure starts when a customer declares they wish to return a product. In addition to a return permission, this step should detail the product’s condition. Additionally, this process involves organizing return shipments, confirming reimbursements, and swapping damaged goods.
2. Deal With Returns:
Examine a returned item once it has been brought to your location or a centralized processing center to determine the category under which it falls. (Note: If your reverse logistics are optimized, you should be aware of where the product must go even before it arrives.) Products should be sorted according to their intended use: repair, resell as new, resell as a return, scrap, recycle, or refurbish.
3. Keep Returns Moving:
Send the repairable products to the department to reduce the waste you produce every day.
4. Repair:
After inspecting it to see if it can be fixed, move the returned item/equipment to the repair area. Sell any items that can be sold if possible.
5. Recycling:
Anything you can’t repair, repurpose, or sell should be delivered to the region for recycling.